Hammer Crusher VS Impact Crusher: Technical Comparison and Selection Guide
In the mining, construction, and metallurgy industries, crushers are essential production equipment, and their choice directly affects the efficiency and costs of production. Hammer crushers and impact crushers are two mainstream products, each with unique technical characteristics and advantages. Below, we will provide a detailed comparison of the two from a technical perspective to help you make a more informed choice.
I. Working Principles and Technical Characteristics
1.1 Hammer Crusher
Working Principle: Materials enter the crusher and are crushed by the impact, shearing, and grinding of high-speed rotating hammers.
Technical Characteristics:
Suitable for crushing materials with medium hardness and below, such as limestone and coal gangue.
Large crushing ratio, typically ranging from 10-25, with some reaching up to 50.
The crushing process involves triple crushing forces, but the main energy consumption is to drive the hammers, achieving energy-saving and consumption reduction.
The particle size of the finished product can be controlled by adjusting the gap of the sieve plate.
1.2 Impact Crusher
Working Principle: Materials are repeatedly impacted and crushed by the high-speed rotating rotor and the impact plate.
Technical Characteristics:
Suitable for crushing high-hardness materials, such as basalt and iron ore.
The impact between materials and materials inside the crushing chamber is more sufficient, resulting in better crushing effects.
The output particle size can be adjusted through various methods such as adjusting the rotor speed and the angle of the impact plate.
The bottom has no grate screen, effectively avoiding clogging when processing wet materials.
II. Technical Parameters and Performance Comparison
1. Crushing Capacity: Impact crushers perform better when processing high-hardness materials, while hammer crushers are more suitable for medium-hardness materials.
2. Output Particle Size: Both can achieve different particle sizes through adjustment, but impact crushers offer more flexibility in adjusting the particle size.
3. Energy Consumption: Hammer crushers achieve energy-saving and consumption reduction through triple crushing, while impact crushers may require more energy when processing high-hardness materials.
4. Maintenance Cost: Hammer crushers have faster hammer wear but a simpler overall structure, making maintenance easier. Impact crushers have a relatively complex structure, resulting in slightly higher maintenance costs.
III. Selection Suggestions
1. Choose based on material properties: For materials with medium hardness and below, select a hammer crusher; for high-hardness materials, choose an impact crusher.
2. Consider production needs: If you are pursuing high efficiency and uniform crushing effects, a hammer crusher is a good choice; if you have higher requirements for crushing effects, you can choose an impact crusher.
3. Comprehensive consideration of costs: When making a choice, it is necessary to comprehensively consider factors such as equipment purchase costs, maintenance costs, and operating costs.
In conclusion, hammer crushers and impact crushers have their own advantages and disadvantages, and the choice of equipment needs to be weighed based on specific needs and actual conditions. Hope the technical analysis and suggestions in this article can provide some help in selecting a crusher.
I. Working Principles and Technical Characteristics
1.1 Hammer Crusher
Working Principle: Materials enter the crusher and are crushed by the impact, shearing, and grinding of high-speed rotating hammers.
Technical Characteristics:
Suitable for crushing materials with medium hardness and below, such as limestone and coal gangue.
Large crushing ratio, typically ranging from 10-25, with some reaching up to 50.
The crushing process involves triple crushing forces, but the main energy consumption is to drive the hammers, achieving energy-saving and consumption reduction.
The particle size of the finished product can be controlled by adjusting the gap of the sieve plate.
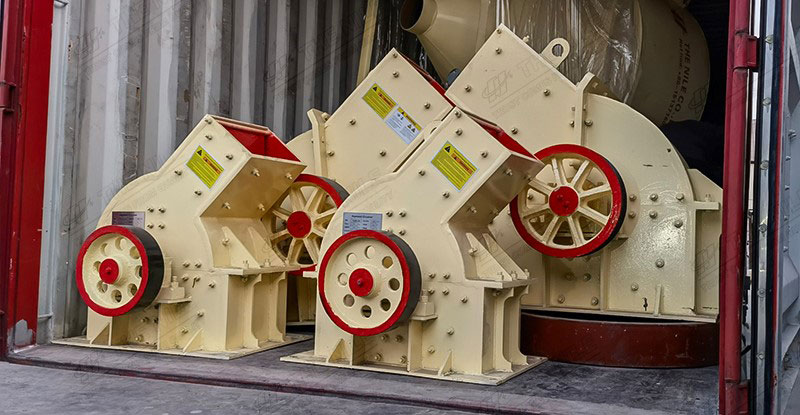
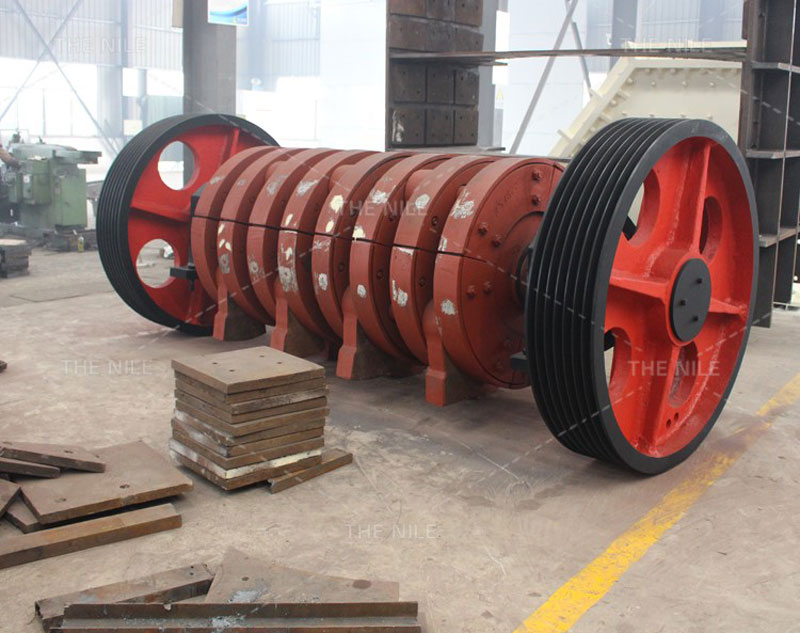
Working Principle: Materials are repeatedly impacted and crushed by the high-speed rotating rotor and the impact plate.
Technical Characteristics:
Suitable for crushing high-hardness materials, such as basalt and iron ore.
The impact between materials and materials inside the crushing chamber is more sufficient, resulting in better crushing effects.
The output particle size can be adjusted through various methods such as adjusting the rotor speed and the angle of the impact plate.
The bottom has no grate screen, effectively avoiding clogging when processing wet materials.
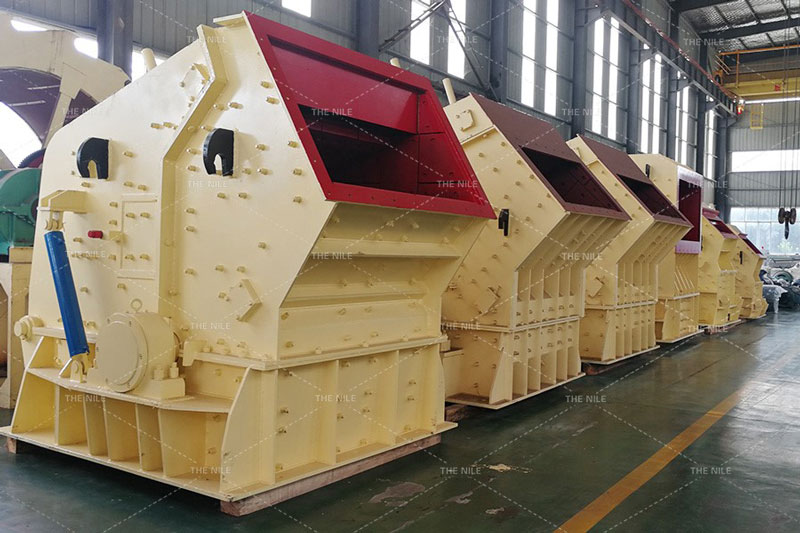
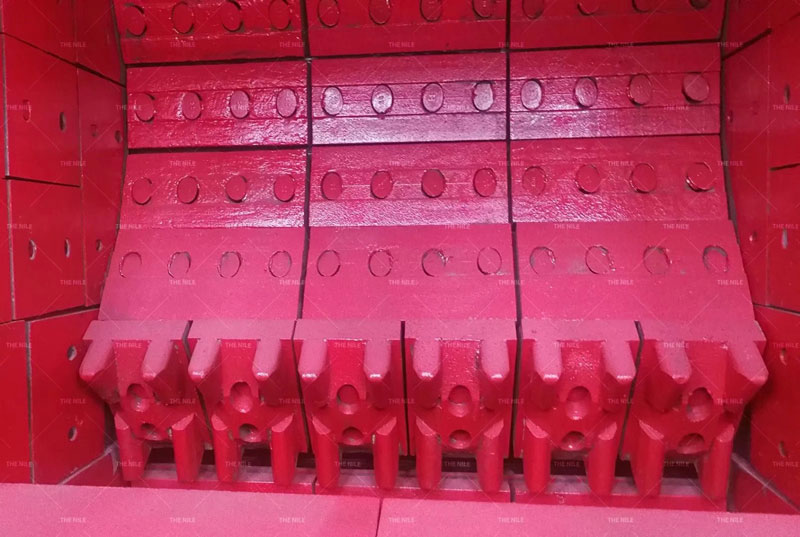
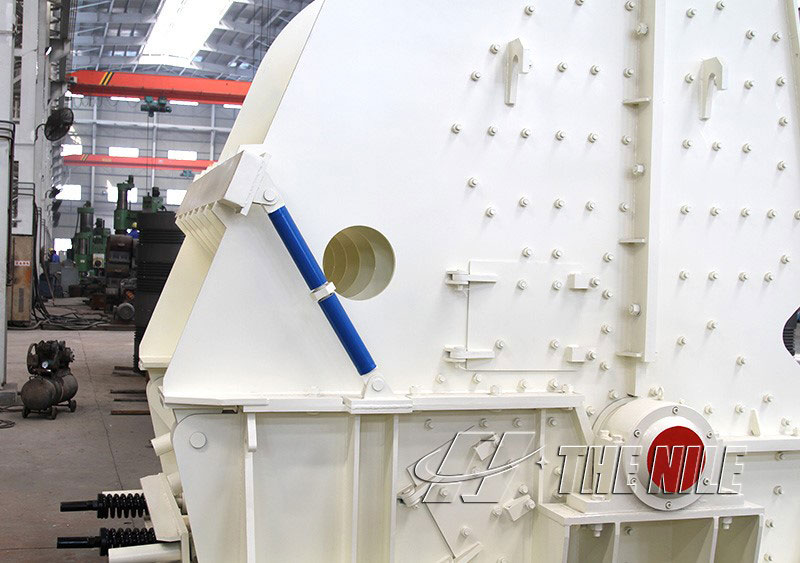
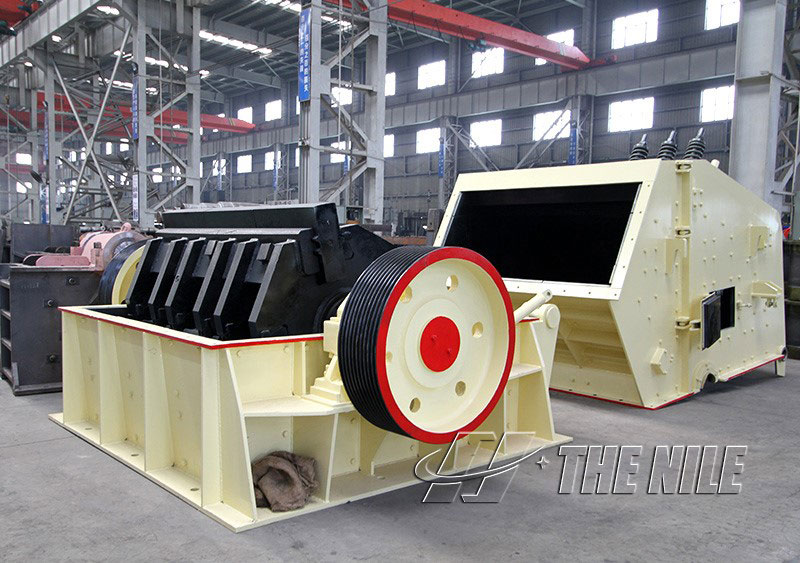
II. Technical Parameters and Performance Comparison
1. Crushing Capacity: Impact crushers perform better when processing high-hardness materials, while hammer crushers are more suitable for medium-hardness materials.
2. Output Particle Size: Both can achieve different particle sizes through adjustment, but impact crushers offer more flexibility in adjusting the particle size.
3. Energy Consumption: Hammer crushers achieve energy-saving and consumption reduction through triple crushing, while impact crushers may require more energy when processing high-hardness materials.
4. Maintenance Cost: Hammer crushers have faster hammer wear but a simpler overall structure, making maintenance easier. Impact crushers have a relatively complex structure, resulting in slightly higher maintenance costs.
III. Selection Suggestions
1. Choose based on material properties: For materials with medium hardness and below, select a hammer crusher; for high-hardness materials, choose an impact crusher.
2. Consider production needs: If you are pursuing high efficiency and uniform crushing effects, a hammer crusher is a good choice; if you have higher requirements for crushing effects, you can choose an impact crusher.
3. Comprehensive consideration of costs: When making a choice, it is necessary to comprehensively consider factors such as equipment purchase costs, maintenance costs, and operating costs.
In conclusion, hammer crushers and impact crushers have their own advantages and disadvantages, and the choice of equipment needs to be weighed based on specific needs and actual conditions. Hope the technical analysis and suggestions in this article can provide some help in selecting a crusher.
Request for Quotation
You can get the price list and a NILE representative will contact you within one business day.