Ball Mill
Ball mill is one of the main equipments in mineral processing plant, responsible for grinding the minerals to suitable particle size for selection before selection, ball mill is also a large proportion of the investment in the whole mineral processing plant, energy consumption of the equipment. Selection needs to be based on the nature of the ore (density, particle size, grade, floatability, mud content), particle size requirements, the size of the plant to determine the selection of a reasonable selection in order to protect the normal production conditions, to achieve energy saving and consumption reduction.
Ball mill according to its application environment, can be roughly divided into three categories: lattice ball mill, overflow ball mill and dry ball mill, in addition to all kinds of ores suitable for the ball mill and rod mill, autogenous mill and other equipment.
Ball mill is the key equipment for crushing materials after they are crushed. Ball mill is suitable for grinding all kinds of ores and other materials, which is widely used in mineral processing, building materials and chemical industry, etc.
The classification situation is roughly as follows:
1. According to the type of grinding and upgrading, it can be divided into:
(1) The medium of the ball mill is metal balls (steel balls or cast iron balls).
(2) The medium of rod mill is steel rod.
(3) The gravel mill uses gravel as the grinding medium.
(4) The self-mill relies on large pieces of ore as grinding medium, and sometimes a small amount of steel balls are added.
2. According to the discharging method, it can be divided into:
(1) The overflow type ore mill freely overflows the slurry through the hollow shaft neck at the discharge end.
(2) The grid type ball mill discharges the material by means of the holes on the grid plate installed at the discharge end.
(3) Peripheral discharge type ore grinding machine discharges materials through the periphery of the cylinder.
Working principle of Ball Mill
Ball mill is a horizontal cylindrical rotating device with outer gear transmission, two warehouses, and a grid-type energy-saving ball mill. The material enters the first bin of the mill uniformly through the feeding device through the feeding hollow shaft spirally. The bin has a step liner or a corrugated liner with steel balls of different specifications. The rotation of the cylinder generates centrifugal force to bring the steel balls to a certain height. After falling, it will have a heavy blow and grinding effect on the material. After the material reaches the rough grinding in the first warehouse, it enters the second warehouse through the single-layer partition board. The warehouse is lined with flat liners and steel balls to further grind the materials. The powder is discharged through the unloading grate plate to complete the grinding operation.
Features of Ball Mill
The intermittent ball mill is composed of feeding part, discharging part, rotating part, transmission part (reducer, small transmission gear, motor, electric control) and other main parts. The hollow shaft is made of cast steel, and the inner lining is removable. The large rotary gear is processed by casting gear hobbing. The cylinder is inlaid with a wear-resistant liner, which has good wear resistance. The machine runs smoothly and works reliably.
Note: According to the material and the discharging method, dry ball mill and wet grid type ball mill can be selected.
Performance
(1) The main bearing adopts large diameter double row self-aligning roller bearing instead of the original sliding bearing, which reduces friction and energy consumption and makes the mill easy to start.
(2) the structure of the end cover of the ordinary mill is retained, and the large diameter inlet and outlet port has a large amount of processing.
(3) the feeder is divided into two types: combined feeder and drum feeder, with simple structure and separate installation.
(4) Without inertia impact, the equipment runs smoothly, and reduces the maintenance time of mill shutdown and improves the efficiency.
Ball mill according to its application environment, can be roughly divided into three categories: lattice ball mill, overflow ball mill and dry ball mill, in addition to all kinds of ores suitable for the ball mill and rod mill, autogenous mill and other equipment.
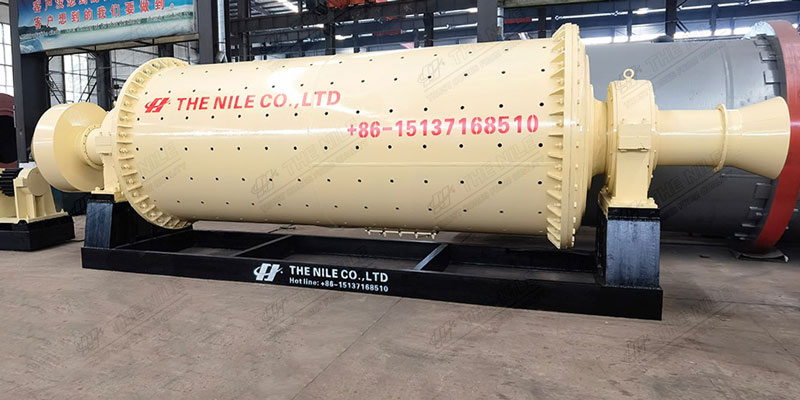
Ball mill is the key equipment for crushing materials after they are crushed. Ball mill is suitable for grinding all kinds of ores and other materials, which is widely used in mineral processing, building materials and chemical industry, etc.
The classification situation is roughly as follows:
1. According to the type of grinding and upgrading, it can be divided into:
(1) The medium of the ball mill is metal balls (steel balls or cast iron balls).
(2) The medium of rod mill is steel rod.
(3) The gravel mill uses gravel as the grinding medium.
(4) The self-mill relies on large pieces of ore as grinding medium, and sometimes a small amount of steel balls are added.
2. According to the discharging method, it can be divided into:
(1) The overflow type ore mill freely overflows the slurry through the hollow shaft neck at the discharge end.
(2) The grid type ball mill discharges the material by means of the holes on the grid plate installed at the discharge end.
(3) Peripheral discharge type ore grinding machine discharges materials through the periphery of the cylinder.
Working principle of Ball Mill
Ball mill is a horizontal cylindrical rotating device with outer gear transmission, two warehouses, and a grid-type energy-saving ball mill. The material enters the first bin of the mill uniformly through the feeding device through the feeding hollow shaft spirally. The bin has a step liner or a corrugated liner with steel balls of different specifications. The rotation of the cylinder generates centrifugal force to bring the steel balls to a certain height. After falling, it will have a heavy blow and grinding effect on the material. After the material reaches the rough grinding in the first warehouse, it enters the second warehouse through the single-layer partition board. The warehouse is lined with flat liners and steel balls to further grind the materials. The powder is discharged through the unloading grate plate to complete the grinding operation.
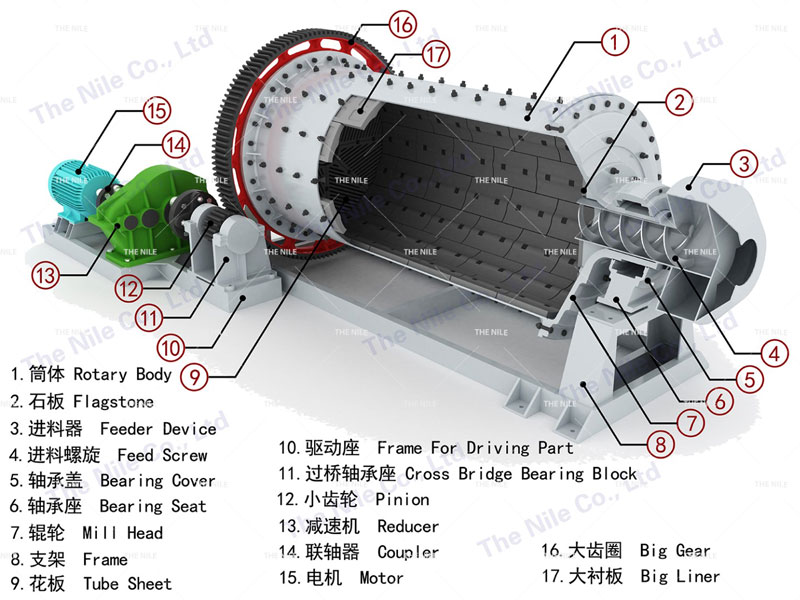
Features of Ball Mill
The intermittent ball mill is composed of feeding part, discharging part, rotating part, transmission part (reducer, small transmission gear, motor, electric control) and other main parts. The hollow shaft is made of cast steel, and the inner lining is removable. The large rotary gear is processed by casting gear hobbing. The cylinder is inlaid with a wear-resistant liner, which has good wear resistance. The machine runs smoothly and works reliably.
Note: According to the material and the discharging method, dry ball mill and wet grid type ball mill can be selected.
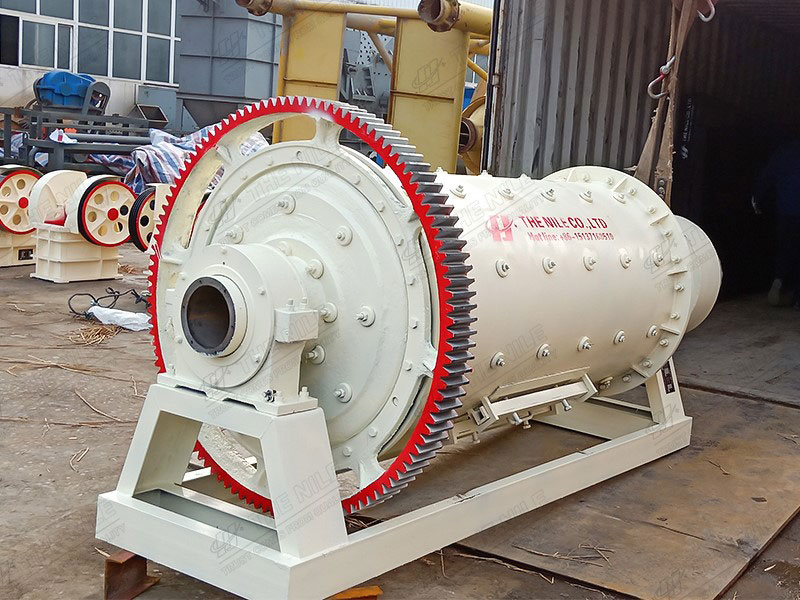
Performance
(1) The main bearing adopts large diameter double row self-aligning roller bearing instead of the original sliding bearing, which reduces friction and energy consumption and makes the mill easy to start.
(2) the structure of the end cover of the ordinary mill is retained, and the large diameter inlet and outlet port has a large amount of processing.
(3) the feeder is divided into two types: combined feeder and drum feeder, with simple structure and separate installation.
(4) Without inertia impact, the equipment runs smoothly, and reduces the maintenance time of mill shutdown and improves the efficiency.
Request for Quotation
You can get the price list and a NILE representative will contact you within one business day.